OHSU Knight Cancer Research Building
Portland, OR
Project Stats
Client
Oregon Health & Science University
Project Status
Complete
Markets
Completed in August 2018, the seven-floor, 320,000-square-foot Knight Center Research Building will serve as a home for up to 650 researchers and staff whose focus is on cancer research and early detection. The building also features wet and dry lab space, administrative offices, a 200-seat auditorium, cafes and ground-floor retail space. It is a “best-in-class” structure designed and constructed to achieve LEED Platinum certification.
The IPD team included OHSU, the Knight Cancer Center, joint venture contractor team McCarthy and Andersen Construction, architect SRG Partnership, Inc., and 10 key trades that were part of our IPD team and early colocation. Upon selection in 2014, the team — owner, contractor and architect — co-located quickly and remained that way throughout the duration of the project. As a result, a tight-knit community developed that served as a melting pot for innovation, cooperation and constant progress toward end goals.
A key aspect is IPD’s ability to help erase boundaries between architects, owners, contractors, key trades and stakeholders. Colocated teams develop better communication habits and can strategically align their goals through group sessions of pull planning and other shared activities.
“One of the things I told (everyone) was you have to be comfortable being uncomfortable,” said Mike Buckiewicz, project manager for OHSU Major Capital Project Design and Construction. “That was a big game-changer because people don’t really like that. They don’t like being uncomfortable and when you push yourself to do that, things come out of it that you don’t typically see.”
Buckiewicz and the team are now firm believers in the power of IPD.
“I truly believe that this is the way of the industry in the future. The new generation coming in is really effective in a more open environment anyway, so to be able to adapt to this is critical.”
The following principles are part of a list that gave the team a ‘north star’ when making decisions about how the building would be designed and how it would perform when occupied.
- Act as an intellectual and social hub
- Be a vertical campus with visual connections to enhance interaction
- Have the ability to be functional and flexible
- Include a primary corridor
- Emphasize shared scientific resources
- Maximize conference and social amenities
- Cluster offices near labs
- Maximize daylight in labs
By focusing on these requirements during the design phase, the provided value to the owner, improved efficiency of decision making, optimized results and reduced waste. This spirit of collaboration that was used by the team building the facility is also being encouraged among the researchers who will be seeking to end cancer working in an environment not segregated by walls or barriers.
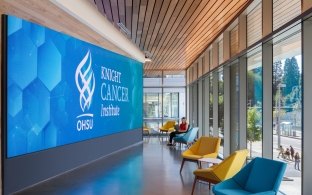
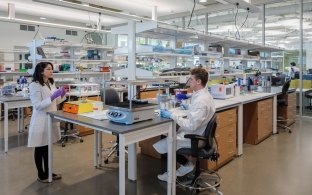
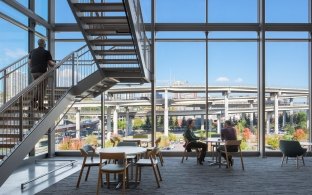
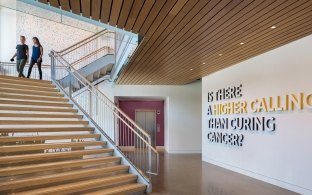
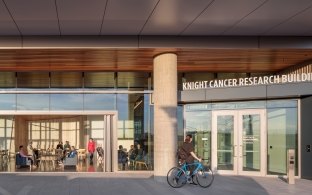
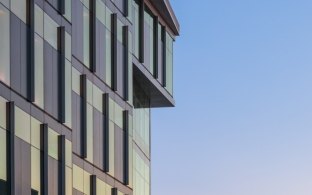
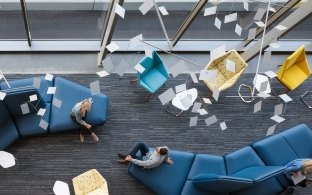
Awards & Recognition
LEED Platinum Certified
2020 Portland's Best Construction Projects of the Decade
Business Tribune
2018 CRE Transformer Award Honoree
Portland Business Journal
2018 CRE Transformer Reader's Choice Award
Portland Business Journal
2018 People's Choice Award
Portland Business Journal
The complexity of cancer research requires integrated, multi-disciplinary teams, and this building is focused on creating the most highly collaborative research environment possible. The design promotes collaborative work and social interaction, which are similar activities, but the distinction is important.
SRG Partnership
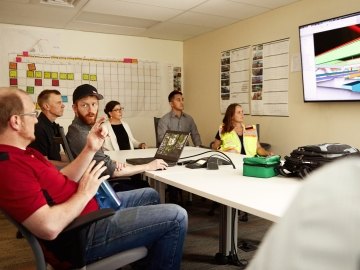
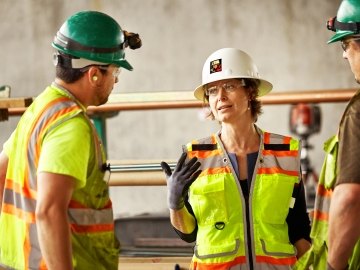
CHALLENGE
The owner and architect wanted to create “neighborhoods” for researchers that help foster work that brings people together, sharing everything from ideas to equipment to personnel.
SOLUTION
Among the guiding principles of the design idea was creating intellectual and social “hubs” on each floor, promoting “spontaneous collaboration.”
“They are collaborating together, they’re not tucked away in offices,” said Laurie Canup of SRG Architects. “They’re sharing resources and they’re working together in a collaborative way to solve cancer.”
CHALLENGE
Aligning all parties in a unique co-location process, hoping to create a more trusting and creative environment.
SOLUTION
Mirroring the collaborative concepts taking place within the facility, the project team employed a similar mindset during the construction process. Armed with a “project-first” philosophy and a concerted design and construction process, the team cultivated an environment based on partnership, innovation and trust. The alignment between parties, coupled with an on-site co-location facility and tools such as virtual reality and lean construction methodology, allowed the team to overcome challenges and deliver an innovative facility that will serve the surrounding community and beyond for years to come.
CHALLENGE
Utilizing Lean construction techniques, including prefabrication, in a tight jobsite area.
SOLUTION
There were duct shafts running vertically the full height of the building. The team was able to coordinate setting the ducts as single pieces for two entire levels at a time. Normally they’d be built piece-by-piece, exposing workers to potential fall hazards, working in awkward positions and sacrificing quality as a result. These ducts were prefabricated off-site, pre-insulated and then flown into position with our tower cranes. This was a huge benefit to the safety of all workers onsite, to the schedule and to the overall project value.
CHALLENGE
Helping stimulate innovative research through highly creative design and architecture.
SOLUTION
Pioneering new concepts in research and science, the Knight Center Cancer Research Building was conceived as a leading-edge laboratory facility that promotes “team science” by encouraging collaborative work and social interaction. The architecturally innovative research building features open air-balconies, communicating stairs, a rooftop terrace and exterior balconies.
CHALLENGE
Place concrete to be prepped for high quality polished finish of over 200,000 square feet of flooring throughout labs and open spaces.
SOLUTION
Collaboration among the team provided the on-site labor and placing, scanning and finishing techniques from similar experience on other projects. McCarthy also brought in industry specialists to help the team understand the science behind placement of concrete with an end product of polished finish, allowing everyone to better understand the steps to a “best-in-class” polished floor.
Joint Venture Partner
Andersen Construction
Architect
SRG Partnership, Inc.