Ameren Bagnell Dam Stabilization
Lake Ozark, MO
Project Stats
Client
Ameren
Project Status
Complete
Markets
The first major structural update to the historic Bagnell Dam in more than 30 years vastly improved the safety and overall stability. The 2,453-foot-long, 148-foot-tall dam not only helped create one of the largest tourist attractions in the state of Missouri — the Lake of the Ozarks — it also is a major source of clean energy that reliably powers homes and businesses throughout the region.
Originally designed in the 1920s, this is an unreinforced gravity dam with three sections and an abutment section that is 1,512 feet long. A highway bridge runs across the top of the dam. Other notable parts of the structure include a 520-foot-long spillway section that includes five sealed sluiceways and 12 floodgates — with each floodgate measuring 22 feet high and 34 feet wide and weighing 54,000 pounds. In 2017, the dam’s Ameren Missouri Osage Energy Center produced more than 624,000 megawatt-hours of energy.
Work began in March 2017 and included the removal of worn and eroded concrete from the surface of the dam. Crews installed 67 post-tension anchors that strengthened the dam’s connection to bedrock below.
We developed an integrated construction solution aligned with Ameren’s expectations and requirements for the dam project. That was followed by executing the safest, high-quality installation that included a detailed approach to quality and safety and the environmental protection plan, logistics and access, aggressive scheduling approach and utilizing value engineering to drive cost reductions.
Hydro-demolition of the back slope area of the dam between the bridge piers was key to the success of the project. A high level of self-perform work helped drive the schedule, retained control of the job and ensured certainty of outcome in all aspects of the project.
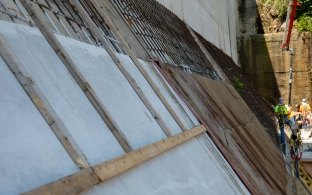
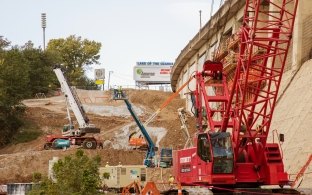
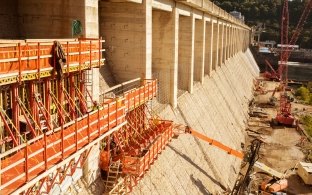
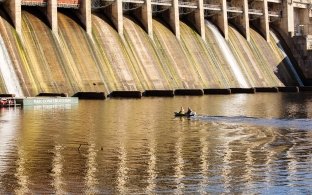
Awards & Recognition
2019 Midwest Safety Award
Award of Merit
Engineering News-Record MidwestSpecial ACI Award
Concrete Council | American Steel Fabrication
American Concrete Institute2016 Keystone Heritage Award
Finalist Industrial Construction
Associated General Contractors, Missouri
Key Success Metrics
- 17,000 cubic yards of concrete (more than 66 million pounds) and 67 post-tension anchors were added as part of the stabilization project.
- There were 27 post-tension anchors and 99 drains located on the west abutment, with 33 anchors and 52 drains located in the spillway.
- Each post-tension anchor has 2 million pounds of holdback capacity.
- In the first 16 months of the project, more than 220 construction jobs were created for local trades and vendors in the region, resulting in an estimated $40 million impact on the area.
Challenges and Solutions
CHALLENGE
Finding a way to remove three inches of concrete from the east and west face sections was a major challenge, as was the logistics of staging cranes and other equipment into an extremely tight jobsite flanked by water, power lines and other obstacles. Making this particularly difficult was the elevation as well as the quantity of concrete removal.
SOLUTION
We turned to Pennsylvania-based hydro demolition services subcontractor Rampart Hydro Services. The company designed and constructed a custom-built robot geared specifically to demolish exterior concrete on the dam’s sloped walls. The robot included a framed water jet and included rubber tires attached to a pulley system, allowing for quick concrete removal.
CHALLENGE
There were six new anchors to be placed on the east section, with 28 on the west section and 33 on the spillway.
SOLUTION
After a previous stabilization project in the 1980s installed 277 post-tension anchors, this time there were 67 — also placed with the latest in technology including sheathed and restressable anchor heads. As a result, each anchor is basically a small hydraulic strand jack, needing at least two grout and redrill cycles to be placed, sometimes as many as five cycles. To guard against corrosion and ensure a long service life, exterior and interior grout, sheathing and epoxy were bonded to the anchor.
CHALLENGE
Since the concrete placed below the vertical portion of the dam was poured diagonally from the top down, some air bubbles got trapped in the concrete and created bug holes.
SOLUTION
Our project engineers determined that Duoguard Formtex was the best solution. It is a flat, permeable formliner constructed to allow water and air to escape while still holding the concrete in. Used primarily in the Netherlands, this not only helped increase the concrete’s density but also created a uniform service. This is the only dam in the U.S. delivering a more durable surface by using a permeable form liner.
CHALLENGE
Another key challenge was the daunting 18-month construction schedule while keeping the road atop the dam open and the power plant’s power generation functional.
SOLUTION
McCarthy, MC Industrial and its subcontractors worked hard during the winter months and holidays to complete the project in a safe and efficient manner. MC Industrial’s Project Tracker — a shared, cloud-based database accessible to all project stakeholders — tracked progress with a simple color-coded system. Project Tracker was used on the dam project to follow progress of concrete lift and placement, rebar and anchor placement and also internal cost reports, including labor and materials. The database contains all project information. so it could easily be accessed by everyone from the owners to engineers and field supervisors.
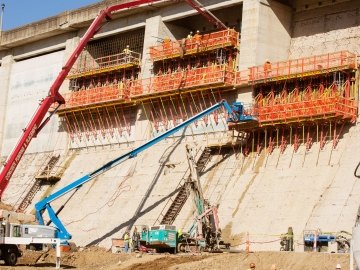
For nearly a century, the Bagnell Dam has reliably powered homes and businesses across the region. These upgrades ensure the dam will continue to be a top producer of clean, renewable energy for Missouri’s communities for the next 100 years.
Ameren Missouri
Results
The installation of 67 post-tensioned anchors drilled from the downstream side of the dam, and placement of mass and overlay concrete to increase the dam’s safety against hydrostatic uplift forces was a success. This ensures long term ability and stability of the dam for years to come, adding the impact of the concrete placed between the highway piers and replacement of worn and cracked concrete on the east and west sections with new concrete overlay.
This project was completed by MC Industrial, a wholly owned subsidiary of McCarthy Holdings, Inc.
TRADE PARTNERS
Brayman Construction
Rampart Hydro Services