Innovative Approach to Prefabrication Yields Efficiencies at New CHI Health Clinic in Omaha
McCarthy Building Companies and Hoefer Welker push the envelope to accelerate the project schedule, save money and streamline on-site labor requirements.
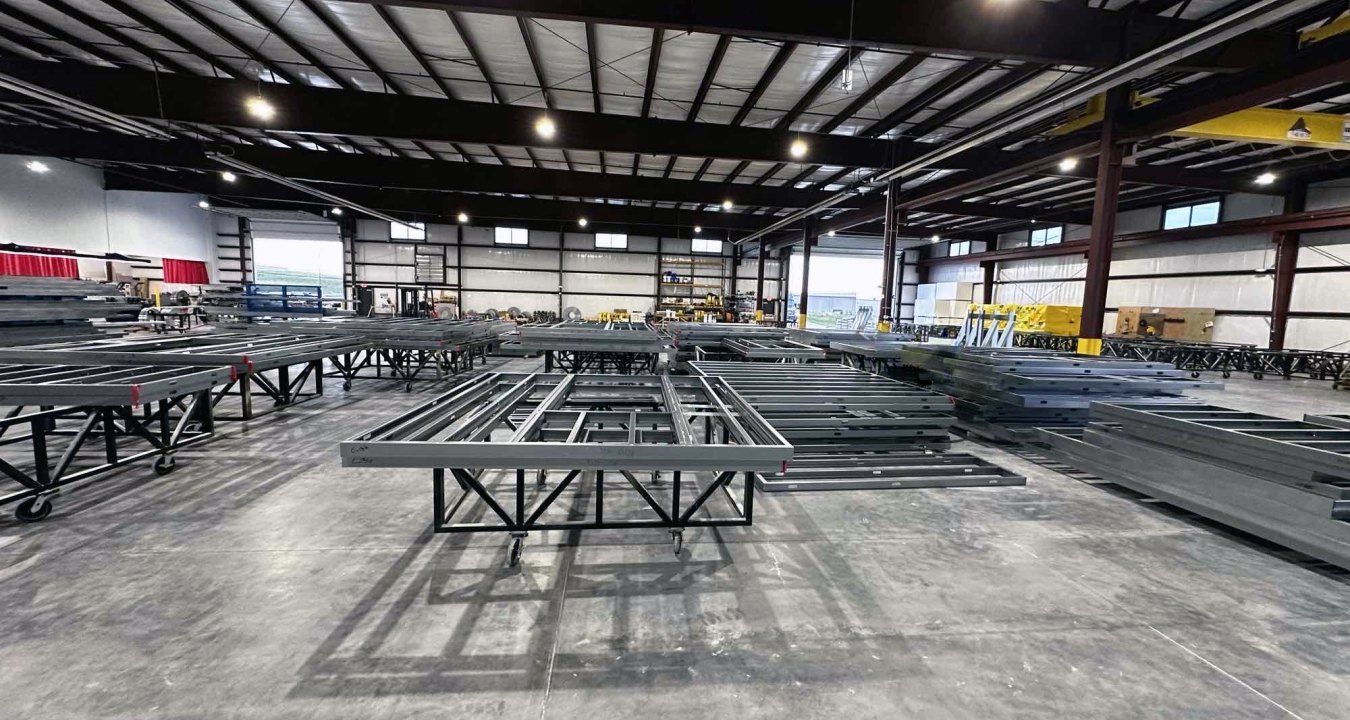
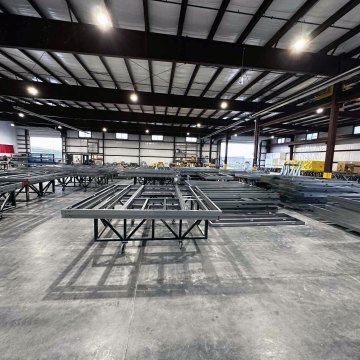
When the CHI Health Immanuel Medical Center Family Clinic opens in summer 2024, patients in north Omaha will have access to exceptional care in a convenient, comfortable environment.
What they may not realize is that they’ll also receive treatment in a high-quality building that was designed and constructed more efficiently than a typical outpatient clinic.
The design-build team of McCarthy Building Companies and Hoefer Welker pioneered an innovative approach to the 40,500-square-foot building that maximizes the use of prefabricated components to unlock impressive project efficiencies.
“All key design decisions were made together with McCarthy to assure we were designing a facility that would improve the overall efficiency of the building process with a focus on reducing construction time, lowering cost, improving quality and reducing waste.”
Partner | Regional Healthcare Practice Leader at Hoefer Welker
The Prefabrication Approach
Because prefabricated components are manufactured in a controlled indoor environment, they can be produced more quickly, precisely and inexpensively than the traditional method of building at the jobsite. Prefabrication also promotes higher quality control standards as building components are manufactured by skilled workers with specialized equipment that ensures accurate measurements, meticulous assembly and rigorous quality checks.
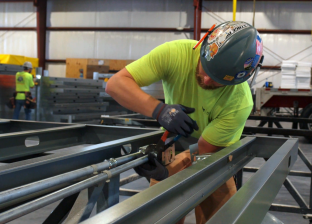
As a result, prefabrication has become an increasingly popular strategy for simplifying the construction of repeatable project elements. But this project goes far beyond a conventional prefab strategy that involves a limited number of components. Instead, the McCarthy team devised an innovative concept that involves prefabricating the majority of the building’s exterior and interior walls.
Bringing this ambitious vision to life required close alignment with the design team to ensure that specific details were jointly planned and incorporated into the design from day one.
Building Information Modeling (BIM) enabled the precise coordination necessary to guide the installation of all prefabricated components.
Specialty contractor Falewitch Construction Services oversaw the construction of the prefabricated wall assemblies. The exterior walls—including framing, sheathing, air and weather barriers—were pre-built in an off-site warehouse. Over 75% of the clinic’s interior walls were also prefabricated off-site. The construction team framed these interior walls and installed electrical conduit, low-voltage conduits, junction boxes and the required blocking and backing to ensure the walls could be quickly set in place inside the clinic, which features an open floor plan.
Accelerating the construction schedule by 10 weeks!
This forward-thinking approach not only accelerated the project schedule, but also reduced the volume—and cost—of drywall and framing materials required to build the job. The team also purchased interior building materials such as studs and electrical devices early to provide cost certainty and avoid potential cost escalation.
Beyond the schedule and cost savings, prefabrication of the walls in a warehouse enabled the construction team to minimize on-site congestion by lowering the total number of tradesperson hours required on the construction site.
The clinic includes 64 exam rooms, treatment rooms, a procedure room, an imaging suite and an onsite pharmacy.
“We mobilized the crane on a Tuesday, and by Friday, the majority of the exterior walls were in place. And we started roofing 14 working days after our first prefabricated panel was set. It was a huge accomplishment.”
Project Manager, McCarthy Building Companies
THE BENEFITS OF PREFABRICATION
60%
FASTER COMPLETION OF BUILDING ENCLOSURE
30%
FASTER FROM START TO FINISH INTERIOR FRAMING
6%
CONSTRUCTION COST SAVINGS OVER TRADITIONAL APPROACH
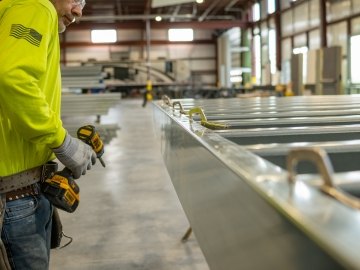