UArizona Applied Research Building Wins Big with Project of the Year at DBIA National
With an impressive year, the University of Arizona’s Applied Research Building (ARB) in Tucson, Arizona, took home multiple awards at November’s 2024 National Design-Build Institute of America (DBIA) conference in Dallas.
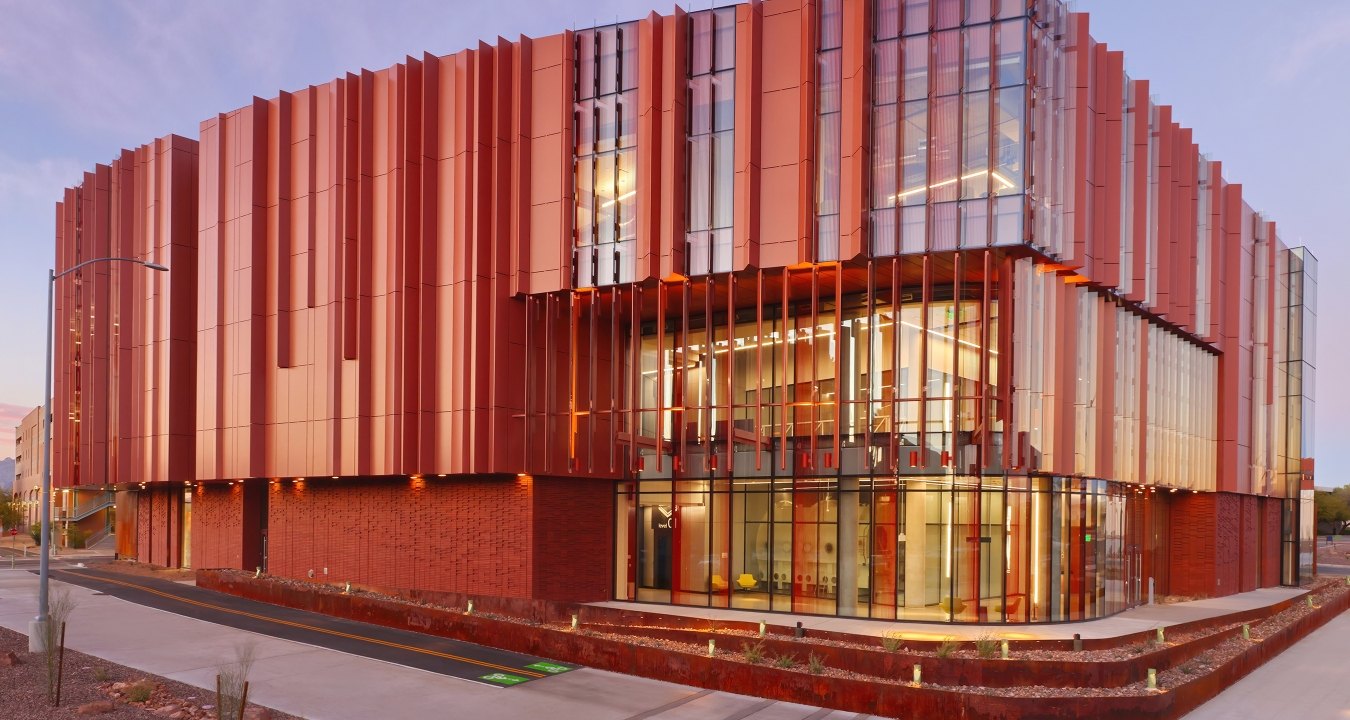
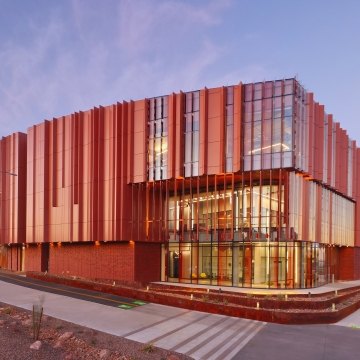
With an impressive year, the University of Arizona’s Applied Research Building (ARB) in Tucson, Arizona, took home multiple awards at November’s 2024 National Design-Build Institute of America (DBIA) conference in Dallas, including Project of the Year, highlighting its successful design and construction amid various pandemic-induced challenges and world-class research components. ARB was also recognized with an Award of Merit and Award of Excellence in the Educational Facilities category.
In May, the team celebrated at the DBIA Western Pacific awards ceremony, with ARB receiving an Award of Excellence for Lean-in Design-Build, an Award of Excellence in Virtual Design and Construction (VDC) and Western Pacific Project of the Year. But what makes this facility so impactful in its use of the design-build delivery method?
One of One — A Unique Facility in the Southwest
ARB is a highly specialized, one-of-a-kind facility that pairs new applied research capabilities with state-of-the-art equipment, technology, and innovative research laboratories to advance research in space exploration, advanced manufacturing, and imaging technology. Uniting eight University departments, the four-story, 89,000 square-foot facility aims to establish the University as a frontrunner in research and testing of satellites, probes, and other spacecraft technologies in lower and upper atmosphere conditions.
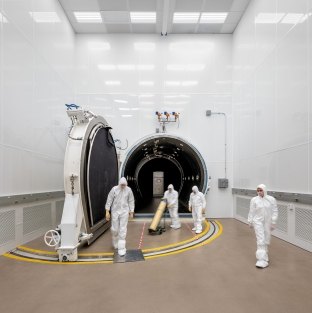
The facility is home to eight unique research components, most notably including the world’s largest thermal vacuum (TV) chamber housed within a collegiate research facility. The 40-ton chamber extends more than 30 feet, with testing capacity for objects nearly the size of a pickup truck. Its function is to simulate both the pressure and temperature conditions found in space, as well as the near-space environment, for testing materials and systems prior to launch in space.
In addition, ARB hosts an anechoic chamber, an echo-free room with radio-wave-absorbing materials to prevent sound waves from bouncing. These conditions allow researchers to test satellite antennae for their command, control, and data relay performance. Finally, within the facility are a laboratory for advanced and additive manufacturing, an imaging technology laboratory, a mission operations center, a CubeSat laboratory, a space materials curation facility, and a high-bay facility with 40-foot ceilings and the nation’s largest custom bi-fold doors.
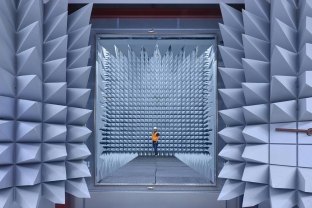
With this facility’s state-of-the-art technology, presenting a design-build solution that adequately represented the grandeur and importance of the facility necessitated McCarthy’s partnership with design partner, SmithGroup. Working in lockstep with the owner, the design-build team, known affectionately as “McCarthy-SmithGroup”, innovatively coordinated the complex building system requirements with the design aimed at putting the “research on display” in establishing ARB as a showcase facility.
A World-Class Space Research Facility Requires Top-Tier Teaming
Immediately upon award, the project team worked with the University’s leadership to identify key stakeholders within each of the parties involved. These included University Planning, Design and Construction, Facilities Management, Office of Research, Innovation and Impact (RII), and the Applied Research Corporation. The design-build team initiated an initial partnering session with stakeholder representatives from each entity to identify Conditions of Satisfaction and metrics that would define success from the beginning of the program validation through commissioning, occupation, and operation of the facility.
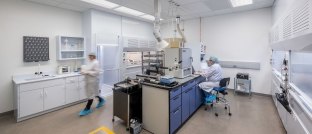
By establishing single points of contact for each stakeholder, the result was a clear level of project ownership, empowerment of the team, and an escalation path in the event roadblocks occurred. Encouraging all team members to have a voice became a precedent that formulated the flat-line leadership and whole-team commitment to a “no one left behind” approach. Due to the early team alignment and detailed communication process, there was no disruption to design development when interaction shifted from in-person to remote due to the global pandemic.
VDC as a Collaboration Lifeline
The use of Virtual Design and Construction (VDC) and Building Information Modeling (BIM) allowed for virtual collaboration through the drawing and approval process, which served as a vital driver of virtual communication to keep the project on track during the pandemic. Both the project team and owner could rely on these tools for coordinating virtual sign-offs for various milestones throughout the project.
Specific VDC deliverables for ARB included:
- Level of Development (LOD) Matrix to capture design-build, design-assist, and trade partner expectations for the model and items that needed to conform to as-built conditions
- Target Clearance Parameters to allow for coordination and proper sequencing of MEP system installation with the University’s facilities management requirements.
- Site Specific Quality Plan fully integrated into ARB’s quality assurance
- Studies of self-shading materials for energy-efficient building design
Most notably, the TV Chamber employed BIM modeling to ensure accuracy in installation and provide as-built conditions to the University. The 80,000-pound chamber arrived with hand-drawn, decades-old drawings with limited detail or use to the team. As a solution, the chamber was laser scanned off-site to produce a BIM federated model for virtual collaboration between trade partners, project team members, and BIM leads in planning the installation. As the crane lifted the chamber into place, the team had the model available through their mobile devices to simultaneously verify positioning with the model. Also shown in the model are the critical MEP scope tie-ins and as-built conditions.
On Time, Under Budget
The project was initially released in 2019 with an intended construction start date in September 2020. However, the University placed the project on a 12-week administrative hold to reevaluate the facility’s programming and funding allocation. Ultimately, the University narrowed down the scope of ARB to serve five distinct needs, but expanded the capacity for each program by 50%. Then, in March of 2020, as the University navigated a full-scale transition to online learning, the design-build team navigated the same transition and uncertainty. Despite both of these pauses to construction, the project maintained its initial schedule duration of 20 months, despite material lead times increasing by six to eight months on average. To ensure the team could begin and end construction at the original duration, the team resequenced procurement packages, GMPs, and design deliverables to limit cost exposure and risk associated with greater material lead times, maintaining continuity of design and construction activities.
The successful implementation of Target Value Design (TVD) allowed the team and university stakeholder groups to effectively manage the design process within budgetary constraints. By engaging in value analysis exercises and exploring alternative design solutions, the team identified opportunities to streamline processes, reduce waste, and eliminate unnecessary expenses without sacrificing quality. In the initial phases of the project, roughly $1.5 million in scope was added to the project. Yet, the team was able to finish below the initial budget, saving roughly 0.78% for the University despite added scope and square footage!
Community Impact
While the University presented no MWSBE requirements for ARB, the team maintained its own goal as part of a greater DE&I and community outreach initiative of bringing in MBE, WBE, and veteran-owned parties to enhance supplier and trade partner diversity. This not only increased opportunities for diverse businesses but also contributed to the economic development of underrepresented communities. The project successfully reached the team’s self-imposed goal of 10% MBE, SBE, and WBE involvement, and 60% local participation, with 80% of ARB’s craft professionals residing in Southern Arizona. ARB also successfully sourced 60% of its trade partners and materials from local Tucson businesses driving economic benefits back into the community.
Research on Display
The Applied Research Building truly speaks for itself in advocation for the complex, best-in-class research happening inside the facility. The open floor plan and glass viewing areas promote public engagement with research, fostering new research opportunities, attracting grant funding, and enhancing the interconnectivity of the diverse programs within ARB. The building’s functionality and utilitarian aspects drove the design, while fitting within the University of Arizona aesthetic on campus. The design team drew inspiration from imagery of payloads, meteorites, satellites, and outer space, while the exterior material palette pulls from the warmth of the Arizona landscape and sleekness of the International Space Station solar array.
With a keen emphasis on sustainability, ARB recaptures all water on site, storing it below grade and filtering it with a series of bio-swales and rain gardens. While ARB’s research requires sophisticated air and exhaust systems, its mechanical systems are designed to be 30% more efficient than the ASHRAE baseline for this building type. A series of localized mechanical rooms serving the needs of the high-demand spaces work in concert with a centralized mechanical penthouse to provide variable ventilation, recirculation, and exhaust recovery. All of these efforts result in a facility achieving LEED Silver.
The accomplishment of this facility in combining five rare and crucial research modules under one university roof will no doubt challenge other Research I institutions in the collective advancement of student involvement in space research. McCarthy is honored to be recognized with SmithGroup for the successful design and construction of such a complex, world-class facility amid multiple pauses, pandemic-induced schedule and procurement challenges. There is nothing like the ARB the building and program are truly unparalleled.