Strategic Benefits of Medical Equipment Planning in Healthcare Construction
Early collaboration between owners, design teams, and construction teams helps reduce equipment-related issues, streamline coordination, and ensure on-time project completion by aligning equipment planning with project schedules.
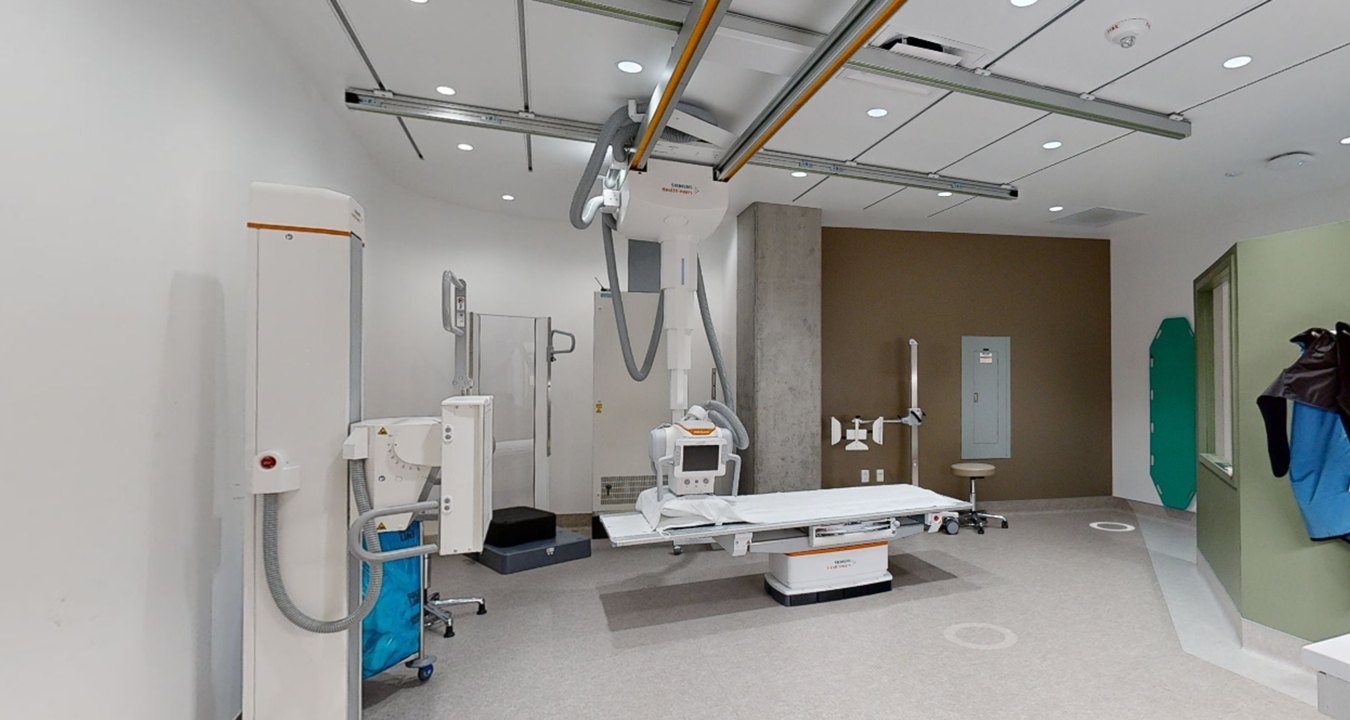
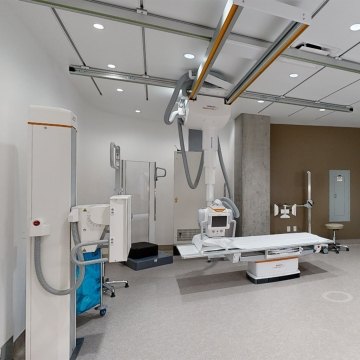
The Right Approach
Far too many owners have had a disappointing experience with medical equipment planning during their construction projects. With equipment planners operating independently from design and construction teams, this approach invariably leads to unforeseen and costly impacts on the project’s building and equipment requirements. Here, we delve into the multifaceted benefits of early equipment planning and procurement services, which is offered by McCarthy EQUIP. The national service offers a full range of equipment related services linking design through final installation and activation.
Early collaboration between owners, design teams and construction teams minimize risks and allow for a seamless integration from design to equipment coordination to construction, resulting in fewer equipment-related project issues, better value, and on-time project completion. By continuously coordinating equipment needs with the project schedule and details, these projects experience radical reductions in unforeseen design changes and change orders stemming from issues including late equipment finalization/selection, procurement/delivery, and availability of critical details needed by the construction team.
Planning
Typically, the design team progresses and completes drawings while the owner/planner engages separately in equipment planning. Often the timing and pace of those activities are misaligned and opportunities to coordinate between the list and the drawings are missed. This process regularly leads to incomplete information in the construction documents and results in redesign and changes down the road, which can lead to significant impacts in the project.
Instead, taking a collaborative approach in the planning and preconstruction with the owner and the design team can help all stakeholders proactively monitor budget, control change, minimize costs, coordinate the details, and manage the design and construction schedule. Engaging experienced medical equipment experts who evaluate and maximize the value of project dollars can mitigate risk and consider future technology as the design and project evolves.
This approach is centered around collaborative work sessions for planning, scheduling, estimating, and driving coordination activities that align with the design schedule. Another condition of success is adopting an owner’s equipment standards, preferences, and current contracts. Integrating these guidelines and merging them with industry knowledge is essential to developing an appropriate equipment list for the project.
For example, McCarthy EQUIP integrates a team of specialists in OR/Interventional Platforms, Radiology/Imaging, and Healthcare Technology Infrastructure in discussions to provide critical evaluations and consider future technology in medical equipment, such as conduits/pathways, boxes and cabling.
Another important relationship to consider for success is equipment planning and the use of BIM (Building Information Modeling). Equipment lists and specifications should not be developed in a vacuum, but instead, equipment planners and BIM coordinators should remain in constant communication. Integrating BIM capabilities into the design process and using the model as “a participant” in design meetings with planners and coordinators provides a real-time picture and central place for coordination and updates.
Managing Risk
Coordination needs to start in the early phases of design. It is crucial to actively look for all the potential conflicts and clashes between the architectural elements and the medical equipment such as space needed to anchor the equipment, counter depth to fit the equipment, etc. Medical equipment planning significantly enhances patient care and safety by streamlining workflows and minimizing errors. This type of coordination in design can help identify any potential conflicts early that can cause changes or delays later during construction.
With the placement of each equipment family in the BIM model, it is important to be mindful of clinical workflow and look for potential clashes with walls, ceiling, millwork components, and design features. Effective medical equipment planning maximizes space utilization within healthcare facilities. To do this successfully, McCarthy EQUIP simultaneously places and coordinates the medical equipment layouts with the architectural background design.
Complete and accurate construction documents are essential for the quality of this project. Page turn reviews, cross checking quotes, drawings, maintaining the database and quality checking vendor drawings are some examples of tools, processes and additional information that help the team deliver a complete and more coordinated set of construction documents. When combining good planning, experience and a collection of tools and proven processes at varying phases of the project, the risks associated with producing medical equipment drawing can be managed.
Future Proofing
In the rapidly evolving realm of healthcare, the integration of advanced medical technology is paramount to delivering superior patient care. Medical equipment planning stands as a cornerstone in ensuring that healthcare facilities are equipped with the right tools, aligning with budgetary and regulatory constraints. This foresight ensures that facilities can adapt to new technologies without incurring significant renovation costs.
As an owner, one of the challenges in equipment procurement is balancing early decisions that still ensure delivery of the latest and most advanced equipment: Do you have the proper budget? What are the unexpected/additional expenses? Will the chosen equipment satisfy project requirements upon arrival?
McCarthy has developed the last responsible moment method, which operates with the evolution of design, construction, and innovation in medical technology. It is not a strategy of delaying commitment – keeping important and irreversible decisions open until the cost of not deciding can become greater than the cost of securing an early decision. Instead, this method provides the owner with the reassurance that they are receiving the latest, state-of-the-art medical equipment for their project.
For final selection, each item is verified with a mandated approval signature prior to ordering. This structure ensures the owner has power of approval, that all stakeholders are operating within the integrated schedules for equipment and construction, and with continuous monitoring to allow for final selection of equipment at the last possible moment. This comprehensive approach ensured that resources were allocated wisely, avoiding unnecessary expenditures and prioritizing critical medical technologies.
Procurement
In any instance when a purchase later got delayed, arrived damaged, or was the incorrect item, unexpected frustration and extra time is needed to correct it. There are always risks with the procurement of goods but imagine the risk and impact that poorly coordinated equipment planning can have on a large-scale, multi-million-dollar project – ranging anywhere from inaccurate needs analysis to lead time uncertainty.
The more complex the project, the higher probability something could go wrong. Employing medical equipment planning can provide more control and certainty during the procurement process.
With EQUIP’s early procurement and risk mitigation services, a team of builders and equipment planners help identify and manage internal and external risks such as scope gaps, process efficiency and redundancy, delays and impacts, and more, ensuring a smooth procurement process.
Leveraging vendor relationships and buying power can also help contribute to enhanced savings. This unique approach throughout the project life cycle minimizes disconnects between equipment planning, procurement, design, and construction teams, aligning with the needs of all stakeholders for seamless project implementation.
Medical equipment planning is more than a logistical necessity; it is a strategic asset that enhances the overall quality and efficiency of healthcare delivery. Engaging in early and strategic equipment planning can optimize resource allocation, ensure regulatory compliance, and prepare for future advancements. By leveraging a collaborative approach, design and construction teams consistently deliver healthcare facilities that meet the highest standards of care. As the healthcare industry continues to evolve, medical equipment planning is an indispensable component of strategic planning and operational excellence to deliver the highest standard of care.
About McCarthy EQUIP
McCarthy EQUIP is a national service that offers coordinated, end-to-end medical equipment planning between owners and design teams. Our focus on seamless integration of building construction and equipment coordination/installation resulting in fewer equipment-related project issues, better value and on-time project completion. EQUIP serves markets such as healthcare, laboratories, government, entertainment and hotels, education and correctional facilities.